Sept 2021 - Present
Background & Overview
UBC Aerodesign is a student engineering design team that designs, manufactures, and flies radio controlled fix-wing aircrafts to compete in the yearly SAE Aerodesign competition. The ruleset changes every three years. The 2022-2024 Advanced Class competition features a firefighting mission profile. The mission includes a main, payload(water) carrying, 120 inch wingspan aircraft that carries a drone, called PADA(Powered autonomous delivery aircraft), and a GTV(Ground transport vehicle). Scoring is based on how much water the main aircraft can carry, how close the PADA can autonomously land itself onto random landing zones, and how much water the GTV can carry to the finish line.
As the co-lead of the Advanced Airfoils team, I oversee analysis, design, manufacturing, and logistics.
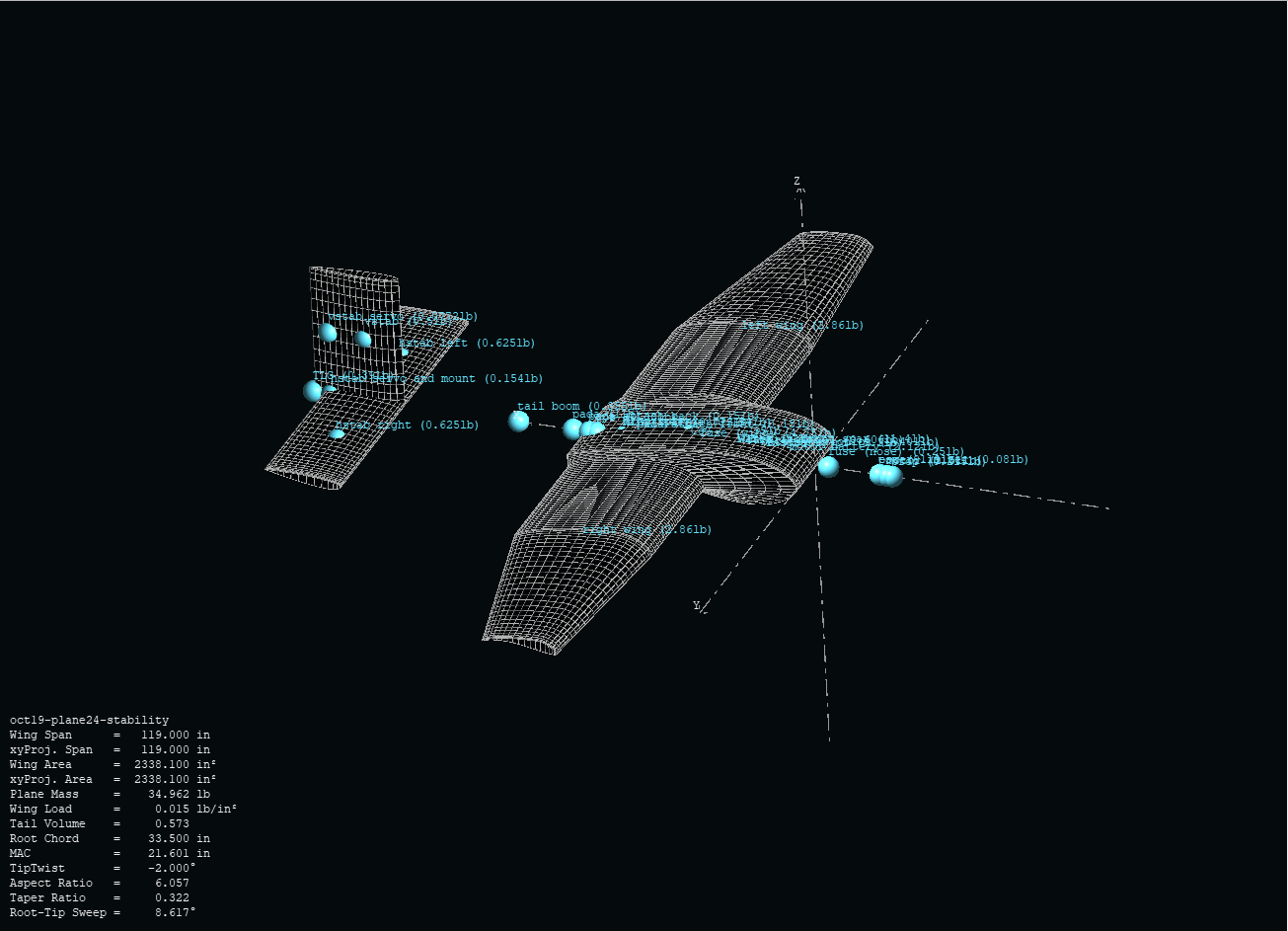
Analysis
- Conducted airfoils and planform analysis in XFLR5 to optimize parameters such as lift and drag
- Verified and cross checked analysis results with SolidWorks Flow Simulation and numerical methods
- Supervised static and dynamic stability analysis and control surface sizing that were done through XFLR5 and Solidworks simulation and numerical methods through spreadsheets
- Conducted structral analysis and material selection with Solidworks FEA to minimize weight while retaining structrual integrity
- Led trade studies to select aircraft configuration to find balance between weight,stability,design feasibility,and cost
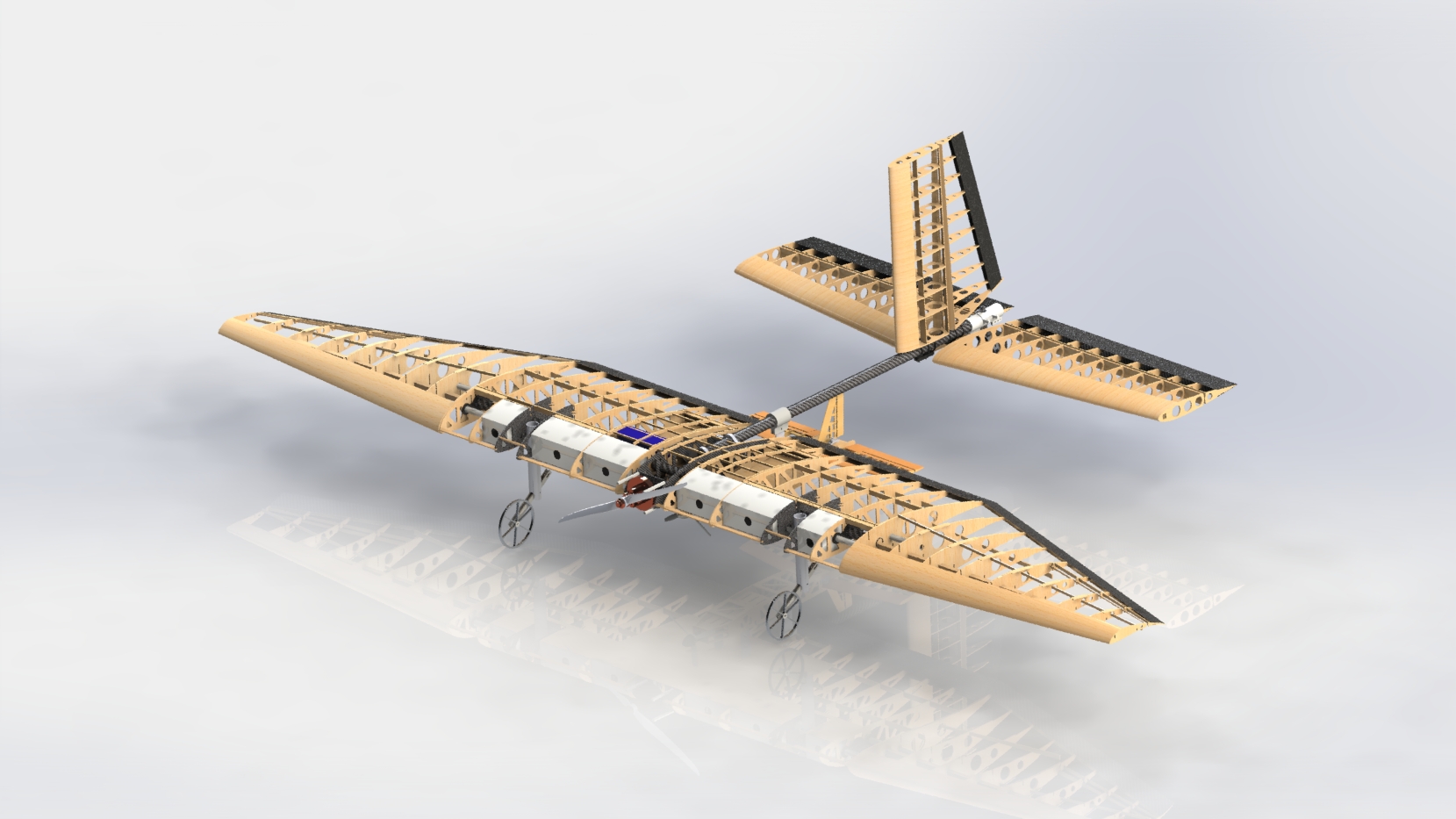
Deisgn
- Designed and modelled the wings and tails in Solidworks with DFMA methods
- Engineered and prototyped interfaces between parts, for example connections between fuselage and wing, tail and landing gear mount, service hatches, control surface connections, electronics and wire housings
- Designed tolerances and alignment features for parts based on types of material used and manufacturing methods
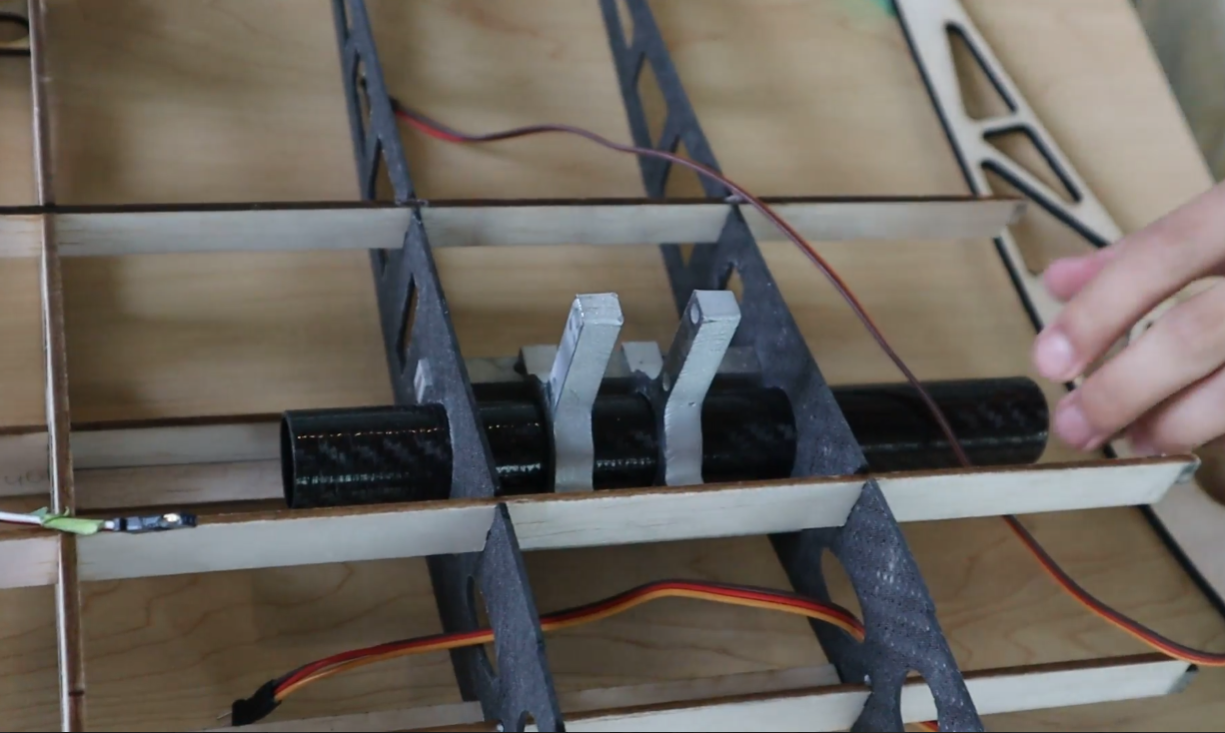
Manufacturing
- Manufactured wood components using lasercutters, carbon fibre and aluminium parts with waterjet cutter, and 3d printed non-planar geometries
- Organized and streamlined production process with effictive use of BOMs, parts labelling, and jigs. Cutting down production time by 70 percent and material waste in half
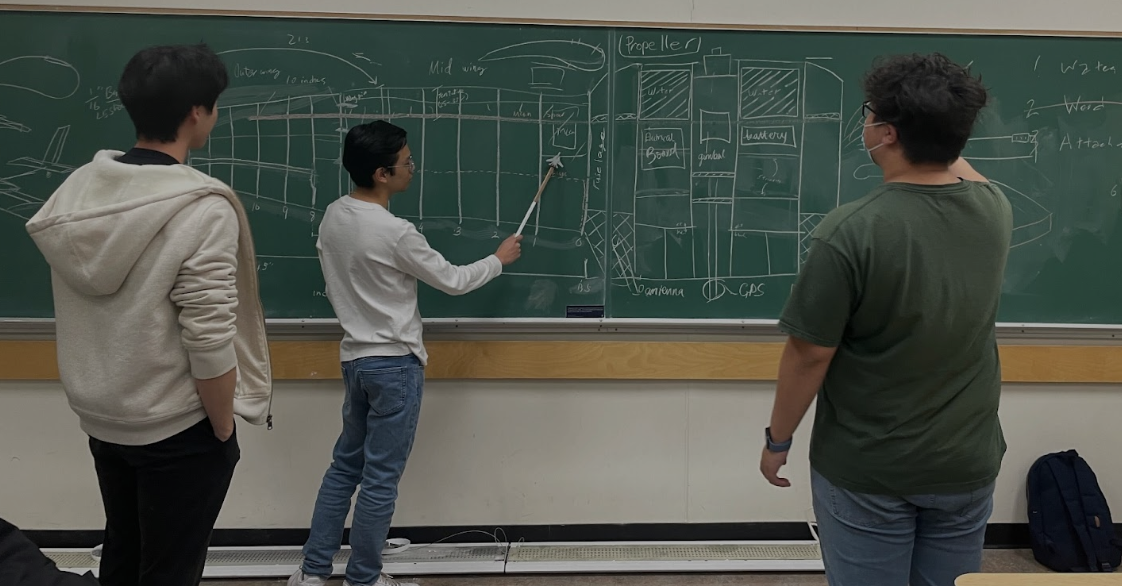
Logistics and Team management
- Evaluated over 100 applications and interviewed 30-40 candidates during two recruiment seasons
- Wrote comprehensive documentation on the design process and manufacturing methods to enable more efficient design verification, cross-subteam communication, and training for new members
- Trained all 10 new members in analysis, design, and manufacturing methods
- Distributed and managed tasks for members to adhere to team timeline
- Presented in team-wide design reviews to ensure effective integration
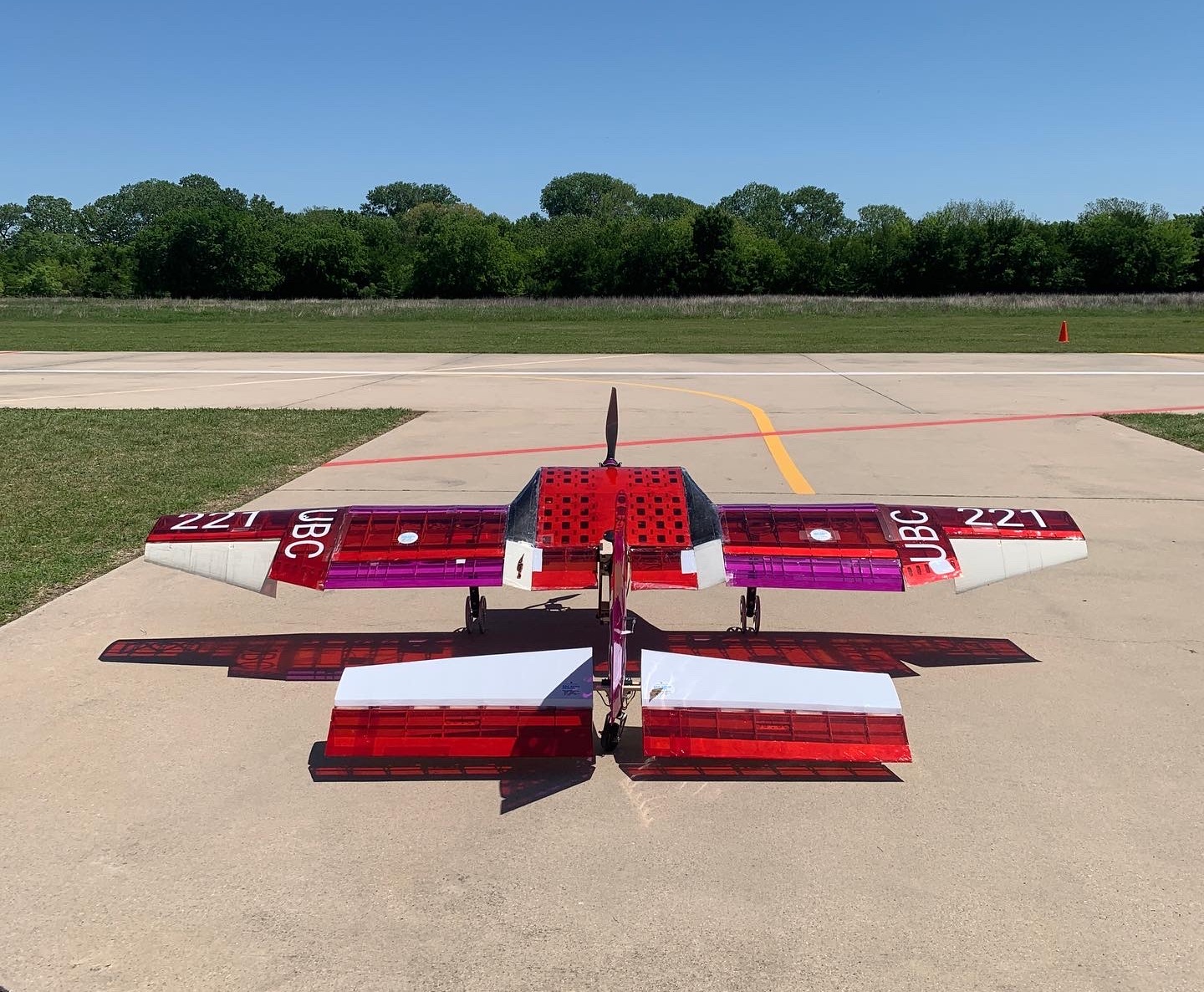
Results
- Produced 4 iterations of the 2022 plane, 3 iterations of the 2023 plane, and 4 iteration of the PADA
- The UBC Advanced Team earned 1st place in the 2023 competition technical presentation
- The UBC Advanced Team earned 5th place overall in the 2022 competition
Images & Videos

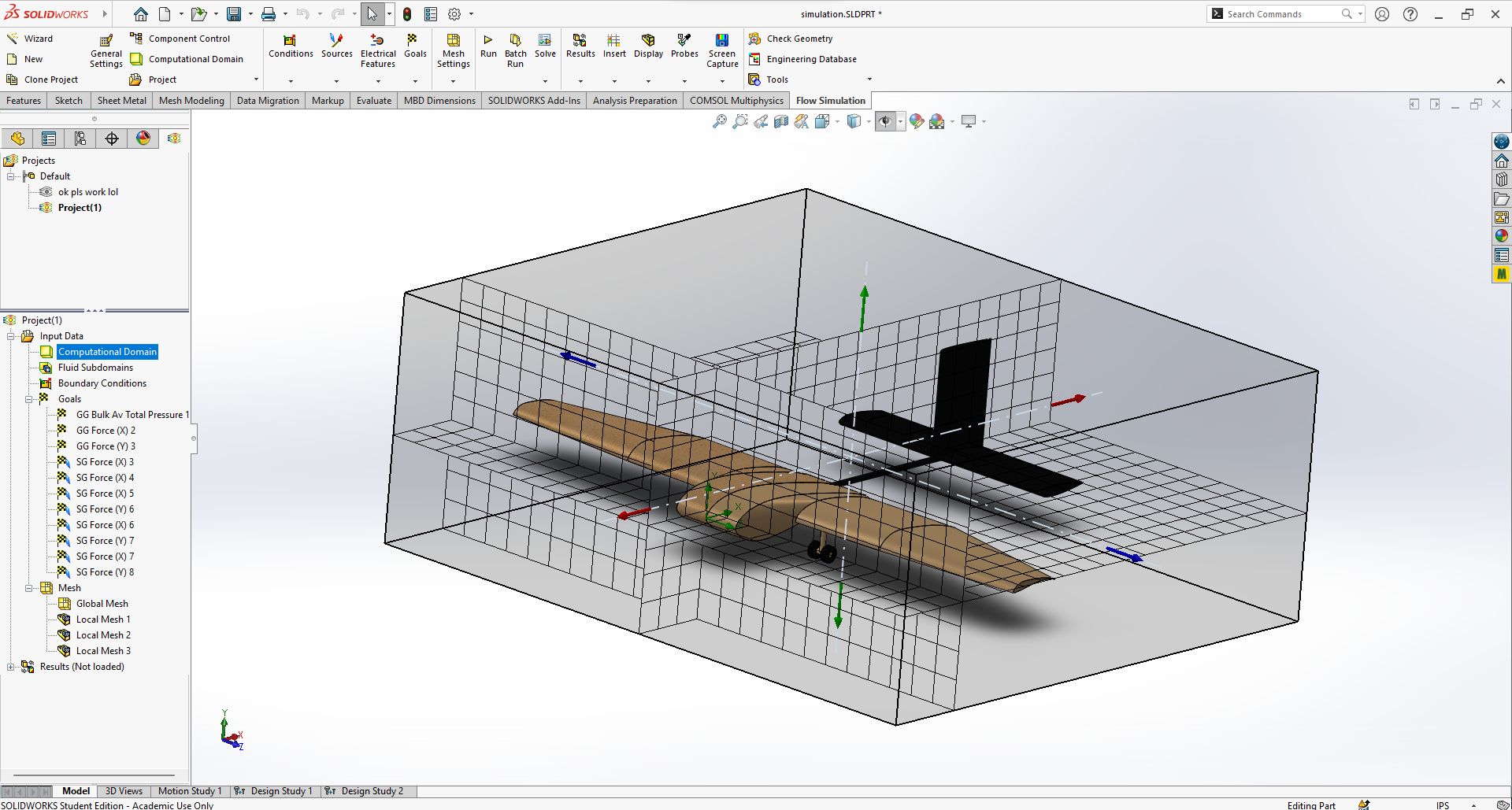
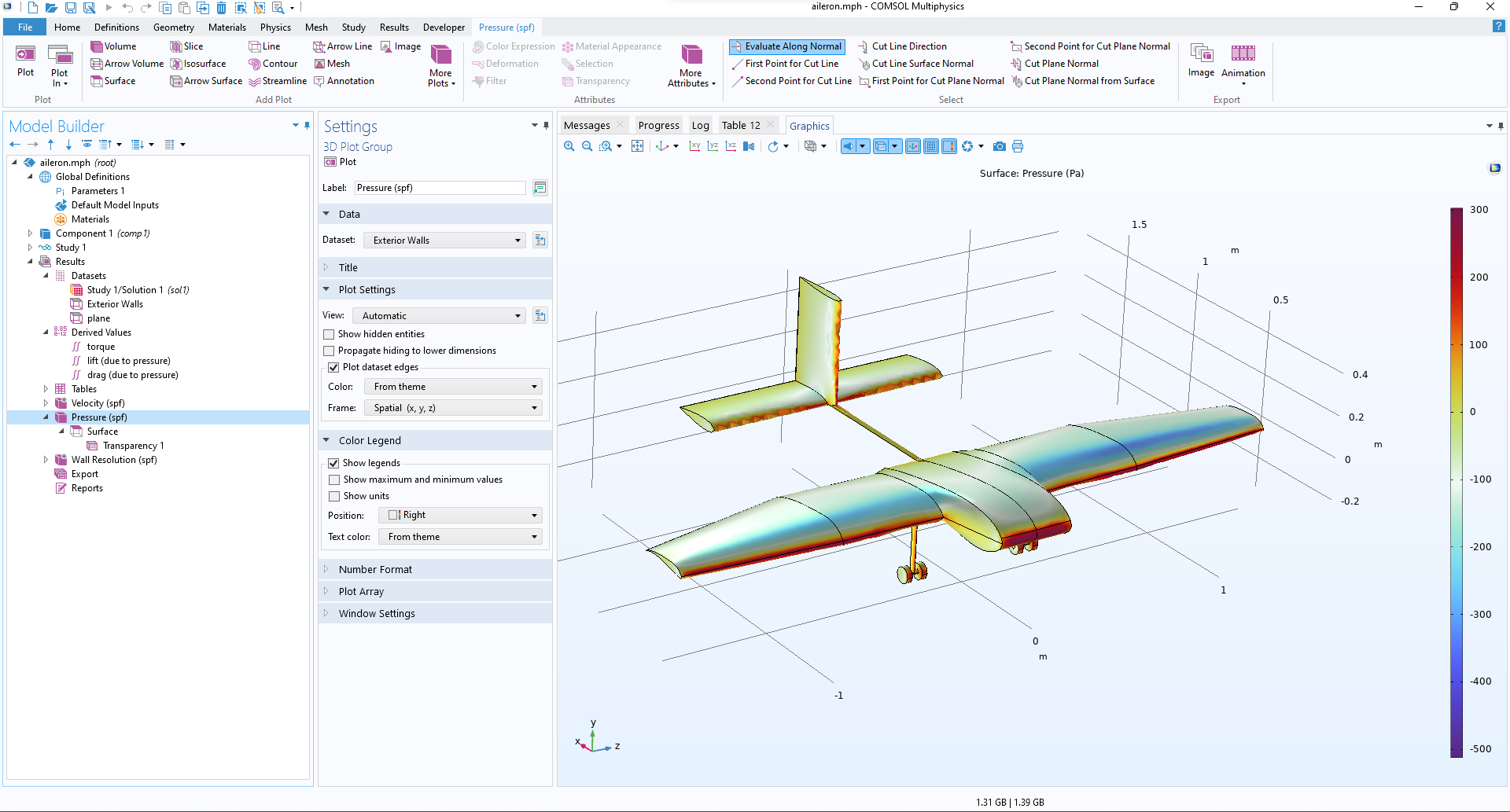
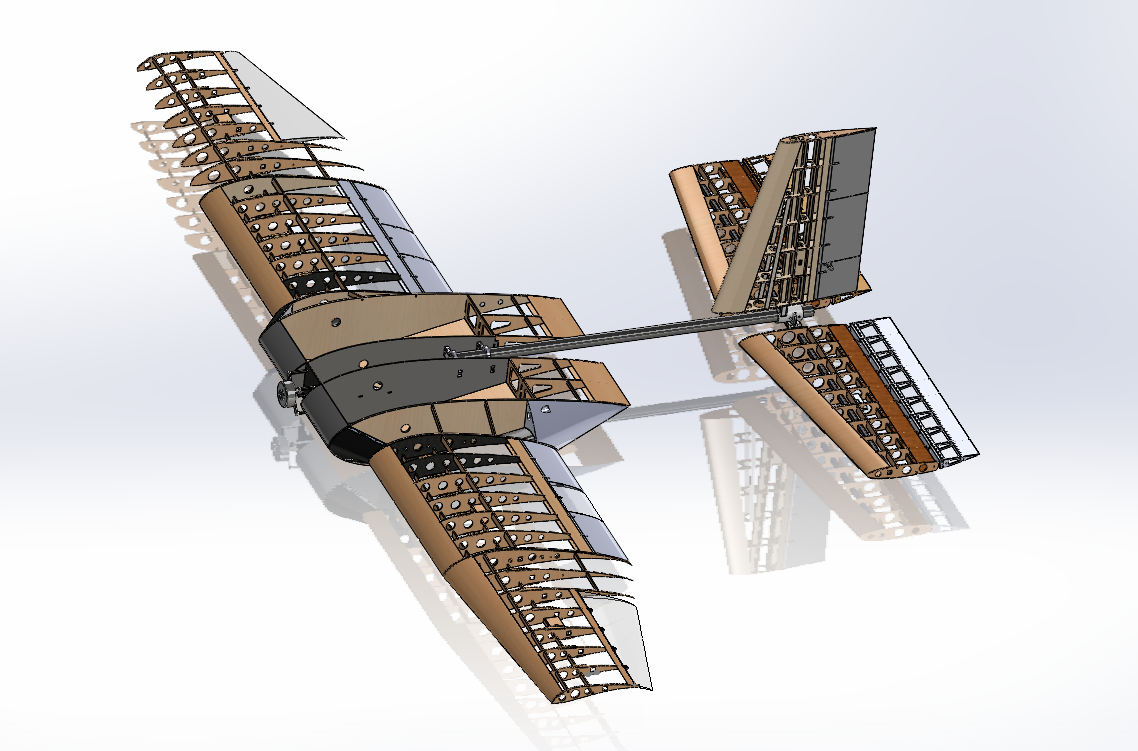